Die Integration von IoT in die Fertigung verändert heute die Branche und treibt einen massiven digitalen Wandel voran. Von der Fertigungsautomatisierung mit Hilfe von Robotern und "Cobotics" - der Zusammenarbeit von Menschen und Robotern - bis hin zur Vorhersage von Anlagenausfällen in der Fabrikhalle und der Verfolgung von Anlagen in einem Lager - die industrielle IoT steht im Mittelpunkt der Zukunft der Fertigung. In diesem Artikel behandeln wir die verschiedenen IoT Anwendungsfälle in der Fertigung und diskutieren zukünftige Trends.
Holen Sie sich unser eBook
Erfahren Sie mehr über Industrie 4.0-Technologie
PDF herunterladen
IoT in der Fertigung
Heutzutage wendet sich jede Branche dem Internet der Dinge (IoT) zu, um Prozesse zu optimieren und zu automatisieren, die Leistung der Edge-Verarbeitung zu nutzen und verwertbare Erkenntnisse aus dem gesamten Netzwerk zu gewinnen. Die Fertigung bildet da keine Ausnahme. IoT in der Fertigung ist ein zunehmender Trend, bei dem die Unternehmen von schnelleren Netzwerken, intelligenteren Geräten und Verbesserungen in der Edge-Technologie profitieren können. In Kombination ebnen diese Technologien den Weg für die Möglichkeiten von Industrie 4.0. Lesen Sie weiter, um mehr über die Anwendungen und Vorteile von IoT in der Fertigung und in intelligenten Fabriken zu erfahren.
Die Auswirkungen von IoT in der Fertigungsindustrie
Industrieroboter sind dank ihrer Genauigkeit, Präzision, Ausdauer und Geschwindigkeit in den Fabriken alltäglich geworden. Jetzt können die Hersteller die Wirkung von Industrierobotern erweitern, indem sie sie mit IoT Geräten verbinden. Die Sensoren von Connected Manufacturing IoT ermöglichen es den Maschinen, miteinander zu kommunizieren, Daten auszutauschen und ihre Aktivitäten selbstständig zu koordinieren. Durch den Austausch von Daten zwischen Maschinen verbessern IoT Geräte die Effizienz und Produktivität von Robotern, während sie gleichzeitig die Sicherheit erhöhen und ungeplante Wartungsarbeiten reduzieren.
Die folgenden Faktoren sind einige der wichtigsten Auswirkungen von IoT im verarbeitenden Gewerbe:
- Effizienz und Produktivität: Einem Bericht von McKinsey zufolge haben die Anwendungen von IoT in der Fertigung das Potenzial, bis 2025 wirtschaftliche Auswirkungen von 1,2 bis 3,7 Billionen Dollar pro Jahr zu schaffen.
- Vorausschauende Wartung: Untersuchungen von Deloitte haben ergeben, dass eine durch IoT ermöglichte vorausschauende Wartung die Zahl der Geräteausfälle um 70 % und die Wartungskosten um 25 % senken kann.
- Energie und Nachhaltigkeit: Der Einsatz von IoT in der Fertigung kann den Energieverbrauch senken. Armal, ein Hersteller von tragbaren Toiletten, stellte beispielsweise fest, dass die Echtzeitüberwachung der Produktionslinie durch IoT dazu beitrug, die Energiekosten der Maschinen um fast 40 % zu senken.
- Optimierung der Lieferkette: Heute suchen 78 % der Führungskräfte in der Lieferkette nach Technologielösungen zur Steigerung der betrieblichen Effizienz, zur Verbesserung der Produktions- und Liefergeschwindigkeit und zur Automatisierung sich wiederholender Aufgaben.

Vorteile von IoT in der Fertigung
Es gibt viele messbare Vorteile von IoT für die Fertigung. Automatisierte Fertigungssysteme sind darauf ausgelegt, komplexe Arbeitsabläufe mit minimalem menschlichem Eingriff zu steuern. Diese Systeme nutzen Spitzentechnologien wie Robotik, künstliche Intelligenz (KI) und intelligente Geräte, um jede Facette des Produktionszyklus zu optimieren. Durch die nahtlose Integration unterschiedlicher Komponenten und Prozesse verbessern automatisierte Fertigungssysteme die Effizienz und Flexibilität erheblich und versetzen Unternehmen in die Lage, die sich wandelnden Marktanforderungen zu erfüllen.
Im Folgenden sind einige der wichtigsten Vorteile von IoT in der Fertigung aufgeführt.
Verbesserte Betriebseffizienz
Durch die Implementierung von IoT können Hersteller mehr Prozesse automatisieren, Anomalien erkennen und Fehler reduzieren und somit die betriebliche Effizienz steigern. IoT ermöglicht Industrierobotern, mithilfe von Sensoren, Kameras, drahtlosen Geräten und Edge Computing autonom zu arbeiten und Aufgaben wie Montage, Fehlererkennung, Sortieren, Stapeln und Routenplanung auszuführen. Intelligente Automatisierung sammelt Daten über Maschinenleistung, Lagerbestände und andere Kennzahlen, die es Herstellern ermöglichen, Prozesse zu optimieren und datengesteuerte Entscheidungen zu treffen.
Vermeidung ungeplanter Ausfallzeiten
Maschinenstillstände können die Produktivität von Fertigungsunternehmen erheblich beeinträchtigen. Einem Analystenbericht zufolge haben 82 Prozent der Unternehmen bereits ungeplante Ausfallzeiten erlebt. Diese ungeplanten Ausfallzeiten können einen Hersteller bis zu 260.000 Dollar pro Stunde kosten, und laut Industry EMEA kosten diese Probleme die Hersteller jährlich etwa 50 Milliarden Dollar. Industrielle Anwendungen des Internets der Dinge stützen sich auf fortschrittliche Sensoren, die Betriebsparameter von Anlagen wie Temperatur, Vibration, elektrische Messwerte und bestimmte Indikatoren für Anlagenausfälle überwachen können, um Fehlfunktionen vorherzusagen, bevor sie auftreten.
Qualitätsverbesserung und Defektreduzierung
Die digitale Transformation und intelligente Fertigungsprozesse können einen großen Einfluss auf die Qualitätsverbesserung haben. Mithilfe von Kameras, Sensoren, KI und maschinellem Lernen können Robotersysteme die Produktqualität schneller und genauer überwachen als das menschliche Auge, Fehler erkennen und schnell reagieren. Einem McKinsey-Bericht zufolge haben Digitalisierung und Automatisierung zu einer Reduzierung der Gesamtabweichungen in der Fertigung um mehr als 65 Prozent geführt. Durch eine schnelle Reaktion können Hersteller Rückrufe aufgrund fehlerhafter Produkte vermeiden, was die Kundenzufriedenheit erhöht.
Verbesserte Sicherheit
Die Automatisierung erhöht die Sicherheit am Arbeitsplatz, indem sie das Risiko von Unfällen und Verletzungen im Zusammenhang mit manueller Arbeit und gefährlichen Aufgaben verringert. Automatisierte Systeme halten sich an strenge Sicherheitsstandards und -vorschriften, verringern das Potenzial für menschliche Fehler und gewährleisten die Einhaltung von Branchenrichtlinien und -protokollen. Heutzutage investieren Fertigungsunternehmen zunehmend in Wearable-Technologien, wie z. B. IoT-fähige intelligente Brillen und Westen, die eine bessere Körperhaltung beim Heben schwerer Lasten unterstützen und vor gefährlichen Verhaltensweisen warnen.
Reduzierte Kosten
Die Automatisierung reduziert den Bedarf an menschlichen Eingriffen bei sich wiederholenden oder arbeitsintensiven Aufgaben, was nicht nur die Arbeitskosten minimiert, sondern auch menschliche Arbeitskräfte freisetzt, die sich auf höherwertige Tätigkeiten wie Problemlösung, Innovation und Prozessoptimierung konzentrieren können.
Da die Wartung von Industrieanlagen fast 70 Prozent der Gesamtkosten ausmacht, sind betriebliche Effizienz und vorausschauende Wartung von entscheidender Bedeutung. Die industrielle IoT Technologie bietet erhebliche Vorteile, wie z. B. die Verbesserung der Fehlerbehebung aus der Ferne und die Verringerung der Anzahl von Serviceeinsätzen, wenn keine Wartung erforderlich ist. Und schließlich ermöglicht der Einsatz von vernetzten Geräten und hochentwickelten Verwaltungsplattformen den Betreibern die Fernverwaltung des Betriebs, einschließlich der Out-of-Band-Verwaltung aus der Ferne.
Skalierbarkeit
Automatisierte Systeme sind von Natur aus skalierbar und können an sich ändernde Produktionsanforderungen und Marktdynamiken angepasst werden, im Gegensatz zu der traditionellen Methode, den Personalbestand zu erhöhen oder zu verringern. Ob es darum geht, das Produktionsvolumen zu erhöhen oder das Produktangebot zu diversifizieren, die Automatisierung ermöglicht es den Herstellern, schnell und effektiv auf sich verändernde Geschäftsanforderungen zu reagieren und so ihre Wettbewerbsfähigkeit und Flexibilität zu erhalten.
IoT Anwendungsfälle in der Fertigung
Die verarbeitende Industrie ist häufig mit Schocks in der Lieferkette, Talentmangel, den Auswirkungen der Inflation und geopolitischer Instabilität konfrontiert. Das Ergebnis ist, dass die Hersteller ständig nach Möglichkeiten zur Kostensenkung und zur Nutzung von Technologien zur Optimierung der Produktion suchen müssen, um die Komplexität und die dynamischen Bedingungen zu bewältigen. Genau hier kann Smart Manufacturing helfen, und deshalb gehören Automatisierung, vorausschauende Wartung, Qualitätskontrolle und Optimierung der Lieferkette zu den wichtigsten Anwendungsfällen von IoT in der Fertigung. Die folgenden Anwendungsfälle veranschaulichen einige wichtige IoT in der Fertigung:
- Fabrikhallen und Felder
- Management der Lieferkette
- Ferngesteuerte Operationen
Intelligente Fabrik IoT für Verkaufsräume und Felder
Von der Automatisierung bis zur vorausschauenden Wartung - alles beginnt mit Sensoren, Kameras, Robotern und intelligenten Geräten wie eingebettete System-on-Module und 5G-Hochgeschwindigkeitsrouter Mobilfunk. In der intelligenten Fabrikautomatisierung steuern diese Technologien in Verbindung mit KI und maschinellem Lernen die Produktmontage, die Verpackung und die Lieferkettenprozesse.
IoT Sensoren für die Fertigung erfassen zusammen mit intelligenten Geräten Maschinendaten wie Temperatur, Spannung, Vibrationen, Luftfeuchtigkeit und mehr für die vorausschauende Wartung. Diese Daten werden vor Ort verarbeitet und analysiert, und die wichtigsten Berichtsdaten werden dann über drahtlose Netzwerke an die Cloud übermittelt. Wenn eine Anomalie erkannt wird, können die Edge-Systeme das defekte Teil herausziehen, die Maschine anhalten oder andere Maßnahmen ergreifen. Dazu gehören die Vorhersage von Ausfällen und das Senden einer Warnung oder eines Service-Tickets an einen Bediener, der die Wartung planen kann.
Ein weiterer wichtiger Fortschritt im Bereich der intelligenten Fabriken ist der Einsatz von digitalen Zwillingen. Dabei handelt es sich um Modelle, die die Fabrikplanung, die Automatisierungsplanung, den Arbeitsablauf und vieles mehr unterstützen und es den Herstellern ermöglichen, komplexe Maschinen und Abläufe zu visualisieren, bevor sie sie in die Praxis umsetzen. In unserem Blog finden Sie Beispiele für digitale Zwillinge.
Hier finden Sie einige Beispiele für Anwendungsfälle und Fallstudien zu intelligenten Fabriken.
- Senkung der Arbeitskosten in der industriellen Automatisierung - Das Unternehmen Honeywell stellt Technologien der nächsten Generation für die Luft- und Raumfahrtindustrie her. Das Unternehmen nutzt die Automatisierung in Produktion und Lagerhaltung, um die Arbeitskosten zu senken und die Gewinnspannen zu verbessern. Von Fördersystemen und Steuerungen, die Materialien durch die Produktion transportieren, bis hin zu Pick-and-Pack-Systemen, Ladern, Palettiermaschinen und Robotern für Distributionsprozesse bietet Honeywell eine breite Palette von Lösungen für Industrie 4.0.
- Senkung der Wartungskosten in der Papier- und Zellstoffindustrie - Das Papier- und Zellstoffproduktionsunternehmen Artesis hat eine Methode zur vorausschauenden Wartung eingeführt, bei der IoT Sensoren eingesetzt werden, um Daten über seine Anlagen zu sammeln und Ausfälle vorherzusagen, bevor sie auftreten. Das Unternehmen senkte seine Wartungskosten um 20 Prozent und steigerte seine Produktionseffizienz um 10 Prozent.
- Die Produktion in der Snackfood-Industrie am Laufen halten - Frito-Lay ist eine der bekanntesten Marken für Snackchips und produziert beliebte Snacks wie Lays, Ruffles, Cheetos und Doritos. Das Echtzeit-Überwachungsprogramm für den Zustand der Anlagen sagt Ausfälle voraus und plant die Wartung, bevor es zu Ausfällen kommt.
Ansicht auf Abruf - Industrial IoT at the Edge: Fernzugriff auf kritische Infrastrukturen
Fertigung IoT für die Optimierung der Lieferkette
Von verpackten Konsumgütern bis hin zu Düngemitteln, Tiernahrung und Ausrüstungsgegenständen - die gesamte Produktion hängt von der Lieferkette ab. Die Bewegung von Waren durch die Lieferkette ist ein komplexer und anspruchsvoller Prozess, bei dem die Hersteller mit einer Vielzahl von Transport- und Bestandsproblemen zu kämpfen haben.
Laut einer Umfrage von Deloitte und der Manufacturers Alliance nannten 56 Prozent der Umfrageteilnehmer den Mangel an Teilen als eine der wichtigsten betrieblichen Herausforderungen. Dank IoT können Supply Chain Manager in der Fertigung einige dieser Herausforderungen angehen. Tatsächlich planen 76 Prozent der Umfrageteilnehmer von Deloitte, sich auf digitale Supply-Chain-Tools zu verlassen, um die Transparenz ihrer Lieferkette zu verbessern.
Hier sind einige der Möglichkeiten, wie IoT in der intelligenten Fabrik und der intelligenten Fertigung zur Optimierung der Lieferkette beiträgt und die Transparenz, Nachverfolgung und Effizienz verbessert.
- Vorausschauende Wartung von Anlagen - Um die Auswirkungen von Transportverzögerungen zu verringern, können sich Supply-Chain-Manager auf IoT Sensoren und Onboard-Kommunikationsgeräte verlassen, um Lastwagen, Schiffe und Flugzeuge auf Wartungsprobleme zu überwachen, bevor diese zu Ausfällen führen können.
- Flottenmanagement - IoT ermöglicht es Transportlogistikmanagern, Engpässe im Fuhrpark zu erkennen, ein wichtiger Aspekt des gesamten Produktionsprozesses.
- Bestandsmanagement - Hersteller können mit Hilfe von IoT Sensoren ihre Lagerbestände optimieren, so dass sie immer über die für die Produktion benötigten Komponenten verfügen.
Autonome mobile Roboter
Seegrid, ein Hersteller von autonomen mobilen Robotern, verwendet hochentwickelte vernetzte Kameras und LiDAR-Sensoren, um gefährliche, sich wiederholende Aufgaben in einer Lagerumgebung sicher zu erledigen.
Echtzeit-Überwachung von Lagerbeständen
Moderne Bestandsverwaltungssysteme nutzen heute Automatisierung und Robotik, um die Bestandsverfolgung in Lagern, Distributionszentren und sogar Einzelhandelsgeschäften zu verbessern. Dank des Echtzeitzugriffs auf den Bestand können Manager bessere Entscheidungen treffen, um die Bestände zu optimieren und einen ausreichenden Bestand zu gewährleisten.
Überwachung des Zustands von Waren im Transit
Um die Qualität zu gewährleisten und strenge Compliance-Anforderungen zu erfüllen, können Hersteller und Spediteure IoT Sensoren und Kommunikationsgeräte einsetzen, um Waren während des Transports zu überwachen und Temperaturen und andere Bedingungen zu melden.
IIoT für Fernoperationen
Industrial IoT bietet Einblicke in das gesamte Gerätenetzwerk eines Unternehmens - egal ob es sich um eine Produktionsstätte, einen ausgedehnten Industriekomplex oder ein Netzwerk mobiler Anlagen wie autonome Fahrzeuge und Drohnen handelt.
Mit den Managementplattformen von IoT , die eine Überwachung der Abläufe in Echtzeit ermöglichen, haben Remote-Teams Augen und Ohren für die Fertigungs- und Industrieprozesse und können den Standort der Anlagen, die Erfüllung, die Auftragsabwicklung, die Betriebszeit und viele andere Faktoren überwachen.
Diese Fähigkeit ermöglicht auch sofortige Warnmeldungen zu bestimmten Bedingungen, vereinfachte Analysen und Berichte, was zu einer Reihe von Vorteilen führt:
- Schnelle Einblicke - IIoT in der Fertigung bietet Betreibern Transparenz im gesamten Netzwerk
- Schnellere Reaktionszeiten - Daten vom Netzwerkrand ermöglichen eine schnelle Reaktion auf Indikatoren an jedem Punkt des Fertigungsprozesses
- Fernüberwachung und -steuerung - Ferngesteuerte Geräte ermöglichen es den Bedienern, automatisierte Eingriffe vorzunehmen, wie z. B. die Anpassung von Durchfluss und Volumen, die Gewinnung von Erkenntnissen für die Fehlersuche und den Neustart von Systemen aus der Ferne
Asset-Verfolgung
Mit Hilfe von Echtzeit-Ortungstechnologien wie GPS, RFID und anderen drahtlosen Technologien können Hersteller den Standort von Anlagen wie Flottenfahrzeugen, Geräten und Materialien schnell ermitteln.
Lagerverwaltung
Eine der leistungsfähigsten Anwendungen der IIoT-Sensortechnologie ist die Möglichkeit, den Zustand von Materialien und Komponenten unabhängig von ihrem Standort in der Lieferkette zu verfolgen. Mit automatisierten Warnmeldungen erhalten die Betreiber sofort eine Benachrichtigung, wenn eine Bestandsunterbrechung vorliegt, sodass sie handeln können, bevor das Problem die Produktion beeinträchtigt.
Energieüberwachung
Die Optimierung des Energieverbrauchs ist ein wichtiger Anwendungsfall in der Industrie IoT . Durch das Hinzufügen von IIoT-Konnektivität zu Maschinen, HLK-Systemen und anderen Geräten, die große Mengen an Energie verbrauchen, können Hersteller den Energieverbrauch optimieren, um nicht nur Kosteneinsparungen zu erzielen, sondern auch Dekarbonisierungsziele zu erreichen.
IoT Herausforderungen in der Fertigung
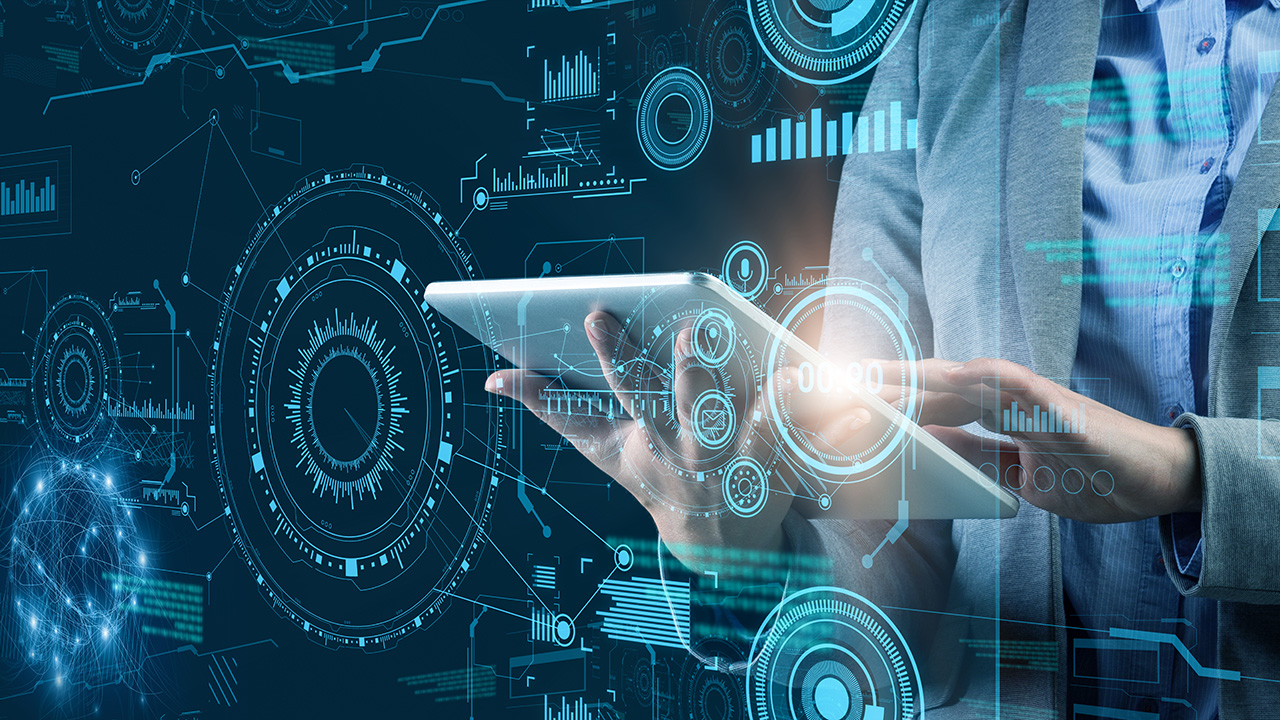
Es liegt auf der Hand, dass IoT einen enormen Mehrwert für die Fertigung bietet. Der richtige IoT Lösungsanbieter kann Ihnen dabei helfen, diese Herausforderungen zu meistern, um sicherzustellen, dass Ihre Implementierung skalierbar, sicher und in die bestehende Infrastruktur integriert ist. Hier sind einige der wichtigsten Herausforderungen, die Hersteller bei der Implementierung von IoT Systemen berücksichtigen sollten:
- Sicherheit - Die Sicherheit bleibt eines der größten Risiken für industrielle IoT Systeme. Hacker, die in eine industrielle IoT Umgebung eindringen, könnten kritische Prozessinformationen stehlen oder verändern, was die Produktqualität gefährden könnte. Für stark regulierte Branchen wie Verteidigung, Gesundheitswesen und kritische Infrastrukturen sind diese Probleme von größter Bedeutung. Wenn die Geräte von IoT nicht ordnungsgemäß aktualisiert werden, stellen Angreifer ein Risiko dar, das von der Unterbrechung des Geschäftsbetriebs bis hin zu enormen Auswirkungen auf Umsatz und Ruf reicht.
- Interoperabilität - IoT Plattformen und Protokolle unterliegen einer Reihe von Standards, was bedeutet, dass Hersteller, Systemintegratoren und Organisationen Interoperabilitätsprobleme bewältigen müssen, wenn sie IoT Geräte in bestehende IT-Systeme integrieren.
- Datenschutz - Durch die Verbindung von IoT Sensoren mit dem Internet sind die Hersteller unmittelbar Cyber-Bedrohungen ausgesetzt, die potenzielle Risiken für den Datenschutz darstellen.
Eine Antwort auf einige dieser Herausforderungen ist ein privates Netzwerk. Heutzutage werden private Netzwerke immer beliebter, da Unternehmen versuchen, die Sicherheit innerhalb ihres eigenen Netzwerks zu gewährleisten und die Servicequalität zu verbessern.
IoT Lösungen für die Fertigung
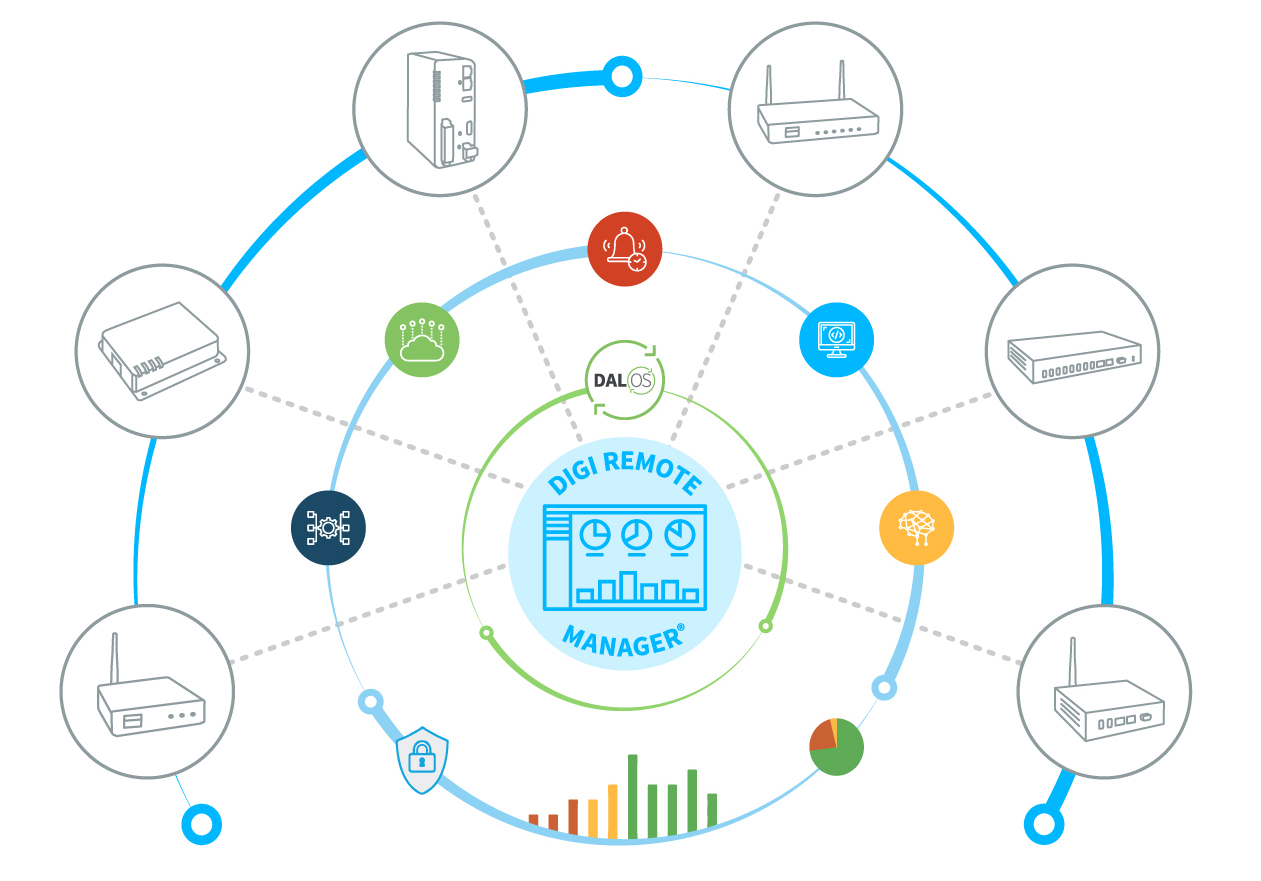
IoT Lösungen für die Fertigungsindustrie bilden das Rückgrat des modernen Fertigungsbetriebs und ermöglichen alles von der Prozessautomatisierung bis zur vorausschauenden Wartung. Die umfassenden drahtlosen Konnektivitätslösungen von Digi lassen sich nahtlos in ein zentralisiertes, cloudbasiertes Softwaresystem integrieren, so dass Hersteller sofort Informationen aus dem Fertigungsbetrieb abrufen können. Ob es um die Überwachung von Anlagen oder die Übermittlung von Firmware-Updates geht, die Fertigungslösungen von Digi IoT helfen Unternehmen, die Wartungskosten drastisch zu senken und gleichzeitig die Produktivität zu steigern.
Digi-Hochleistungsrouter Mobilfunk
Digi ist seit 1985 ein Anbieter von Konnektivitätslösungen, der die kritischen Anforderungen von Organisationen in den anspruchsvollsten Anwendungsbereichen unterstützt, von industriellen Operationen bis hin zu medizinischen Anwendungen und Notfalleinsätzen, und wir erweitern ständig unser Portfolio an Hochleistungsroutern Mobilfunk für Anwendungsfälle in Unternehmen, der Industrie und im Transportwesen.
Eine unserer neuesten Ergänzungen zu diesen IoT Lösungen für Fertigungs- und Industrieanwendungen ist Digi IX40, eine 5G-Edge-Computing-Lösung, die speziell für Industrie 4.0-Anwendungsfälle entwickelt wurde. Diese Lösung bietet globale 5G- und LTE-Unterstützung und ist für die wichtigsten Betreibernetzwerke auf der ganzen Welt zertifiziert. Darüber hinaus unterstützt sie Digi Containers , um leistungsstarke, kosteneffiziente Anwendungen am Netzwerkrand zu ermöglichen.
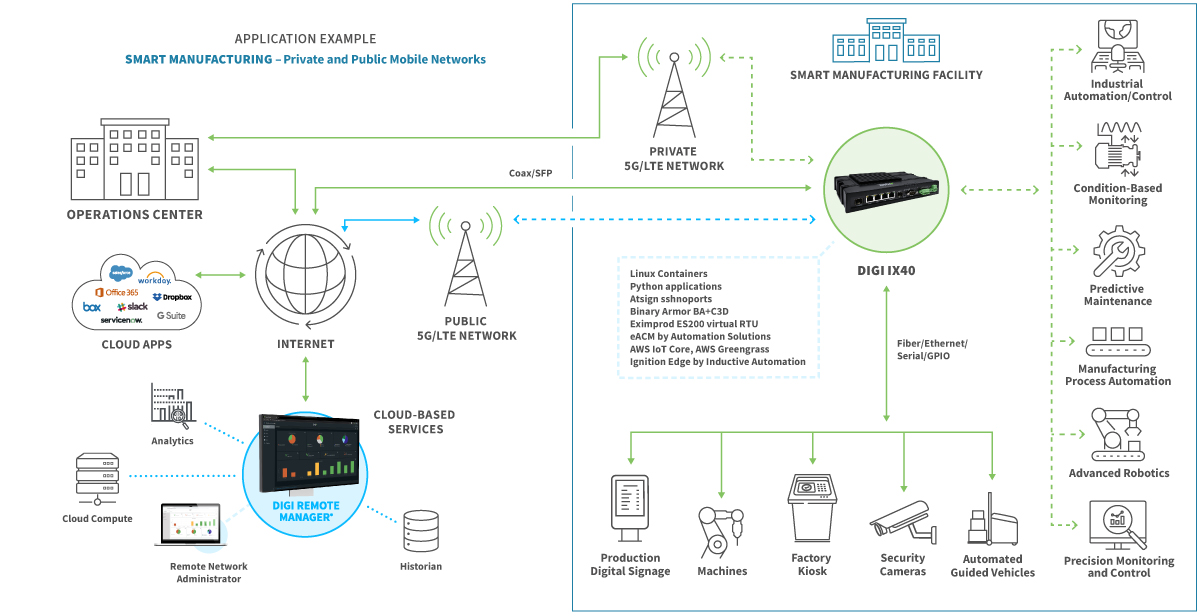
Digi Embedded Systems für Entwickler
OEMs, die Lösungen für IoT auf dem Fertigungsmarkt entwickeln, benötigen eine Reihe von eingebetteten Lösungen. Digi bietet zwei komplette Entwickler-Ökosysteme an:
- Das Digi XBee® Ökosystem von drahtlosen Kommunikationsmodulen, Tools und Dienstleistungen: Diese kostengünstigen Kommunikationsmodule bieten drahtlose RF- oder Mobilfunk -Konnektivität, wenn geringer Stromverbrauch wichtig ist. Digi XBee Module sind vorzertifiziert, einfach zu implementieren und können schnell mit lokalen Tools wie Digi XCTU® und Digi XBee Studio oder für die netzwerkweite Implementierung mit Digi Remote Manager konfiguriert werden.
- Das Digi ConnectCore® Ökosystem von System-on-Modulen, Tools und Dienstleistungen. Das umfangreiche Angebot von Digi ConnectCore umfasst SOMs, SBCs, Code-Bibliotheken, Sicherheits- und Fernverwaltungsdienste und vieles mehr. Die leistungsstarken Digi ConnectCore SOMs beinhalten die neueste Technologie für Edge Computing, schnelle Entwicklung und Time-to-Market, zusammen mit einer kompletten Suite von Tools und Ressourcen für skalierbares Design und einfache Wartung.
Digi IX15 IoT Gateway und Mobilfunk Router
Einige industrielle Fertigungsprozesse stellen aufgrund der rauen Umgebungsbedingungen besondere Anforderungen an die IoT Kommunikation. Digi IX15 ist ein industrietaugliches IoT Gateway mit Class 1 Division 2 Einsatzzertifizierung und einem robusten Gehäuse, das speziell für raue Umgebungen entwickelt wurde. Es lässt sich nahtlos in das Digi XBee Ökosystem und die Digi Remote Manager integrieren, um die Effizienz zu steigern, egal ob Sie Dutzende oder Tausende von Geräten einsetzen.
Digi Connect Sensor+ mit Digi Remote Manager
Der Digi Connect Sensor+ mit Digi Remote Manager ist perfekt für die Fernüberwachung in rauen Umgebungen ohne einfachen Zugang zu Strom. Die einfache Installation, die Zuverlässigkeit und der geringe Datenverbrauch machen Digi Connect Sensor+ zu einer großartigen Lösung für die Fernüberwachung in Bereichen, in denen IoT bisher zu kostspielig war.
Begleiten Sie die Zukunft von IoT in der Fertigung mit Digi
Von der Verbesserung der Prozesssteuerung über die Fertigungsautomatisierung bis hin zur Robotik: IoT in der Fertigung schafft Effizienz- und Produktivitätssteigerungen entlang der gesamten Wertschöpfungskette. Die Implementierung von IoT in der Fertigungsindustrie erfordert jedoch spezielles Fachwissen. Aus diesem Grund ist es wichtig, mit Experten zusammenzuarbeiten.
Digi bietet seit 1985 drahtlose Kommunikationsdienste an und ist seitdem gewachsen, um Anwendungen für die gesamte IoT Landschaft anzubieten. Da sich die Hersteller auf eine stärker digital integrierte und vernetzte Zukunft vorbereiten, die unglaubliche Effizienz- und Produktivitätssteigerungen verspricht, benötigen sie sichere, zuverlässige und skalierbare Lösungen. Genau hier kann Digi helfen. Unsere komplette Netzwerkinfrastruktur, Konnektivität und Fernverwaltungslösungen helfen Herstellern, die Effizienz und Produktivität zu erreichen, die sie sich für die Zukunft von IoT in der Fertigung vorstellen.
FAQs für IoT in der intelligenten Fertigung
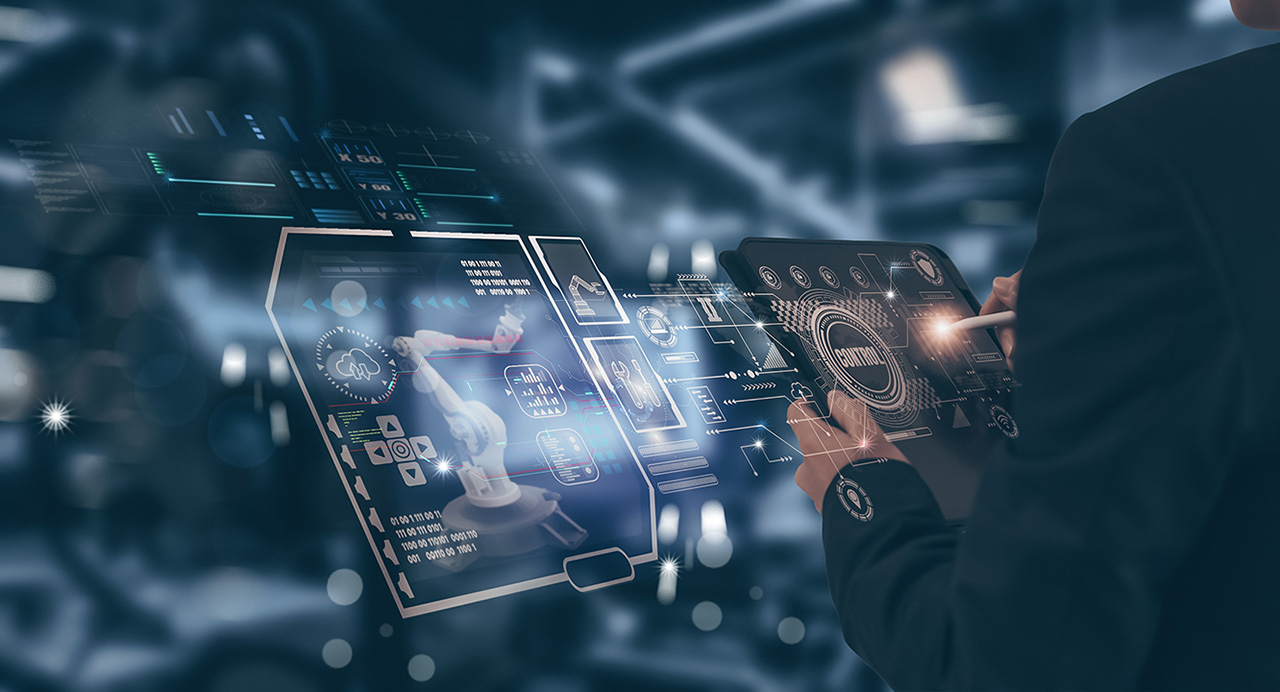
Wie wird IoT in der Fertigung eingesetzt?
In der Fertigungsumgebung IoT bezieht sich der Begriff IoT auf das Netzwerk von Sensoren und Geräten in einem Fertigungsbetrieb. Denken Sie an Maschinen, Lagerroboter, Fahrzeuge und Inventar, die alle Daten über eingebettete Geräte, Router und drahtlose Netzwerke senden und empfangen. Da alles über 5G-Hochgeschwindigkeitsnetze verbunden ist, entsteht eine ganz neue Welt der intelligenten Industrie IoT .
Welche Probleme lösen IoT und intelligente Sensoren für Fabriken?
Wenn Hersteller zur Nutzung von IoT analytics übergehen, eröffnen sich ihnen zahlreiche Vorteile, z. B. die Möglichkeit, Trends zu erkennen, sofort zu handeln, um Ausfälle zu reduzieren und Einblicke in die Optimierung der Abläufe zu gewinnen. Infolgedessen schafft IoT in Fabriken durch Sensoren und Datenanalyse einen Mehrwert auf der ganzen Linie.
Wie können IoT Geräte die Ausfallzeiten in einer Fertigungsanlage minimieren?
Vorausschauende Techniken helfen bei der Erkennung potenzieller Ausfälle und ermöglichen es den Betreibern, ungeplante Ausfallzeiten zu vermeiden, indem sie Wartungsarbeiten einplanen, bevor es zu Ausfällen der Anlagen kommt. Auf diese Weise ist es weniger wahrscheinlich, dass die Anlagen während der Produktion ausfallen, was die Ausfallzeiten minimiert.
Wie kann die IoT die physische Sicherheit in der Fertigung verbessern?
Das Internet der Dinge in der Fertigung nutzt Sensoren, um unsichere Betriebsbedingungen zu erkennen und die Arbeiter zu warnen, bevor es zu einem Unfall kommt. Von Panikknöpfen und intelligenten Alarmen bis hin zu intelligenten Leuchten und IoT Wearables gibt es viele Möglichkeiten, wie IoT Geräte dazu beitragen, Menschen vor potenziellen Gefahren in der Fabrikhalle zu schützen.
Wie kann die IoT die vorausschauende Wartung in der Fertigung verbessern?
Bei IoT und in der Fertigung steigert die vorausschauende Wartung den unmittelbaren Wert, indem sie die Effizienz der Anlagen verbessert und die Wartungskosten minimiert. Dank IoT ermöglicht die Datenerfassung fortschrittlichere Anwendungsfälle für die vorausschauende Wartung.
Wie verändert IoT die Luft- und Raumfahrtindustrie?
Mit IoT in der Fertigungsindustrie können Überwachungs- und Steuerungstools am Fließband in der Luft- und Raumfahrtindustrie die Qualität und Produktivität um bis zu 30 Prozent verbessern. IoT und die dazugehörigen fortschrittlichen Algorithmen können sogar dazu beitragen, den Energieverbrauch in der Flugzeugproduktion zu optimieren und den Energieverbrauch um bis zu 20 Prozent zu senken.
Wie können Hersteller PCBs für ein besseres IoT Design optimieren?
Jedes IoT Gerät hat eine Leiterplatte (PCB). Um eine Leiterplatte für ein besseres IoT Design zu optimieren, sollten die Hersteller die Platzierung der Sensoren sorgfältig berücksichtigen, um die Signalintegrität zu erhalten. Bei der Entwicklung und Herstellung der elektrischen und mechanischen Aspekte von IoT Geräten sollte alles berücksichtigt werden, von den verwendeten Materialien bis hin zur Art der Anwendung.
Nächste Schritte